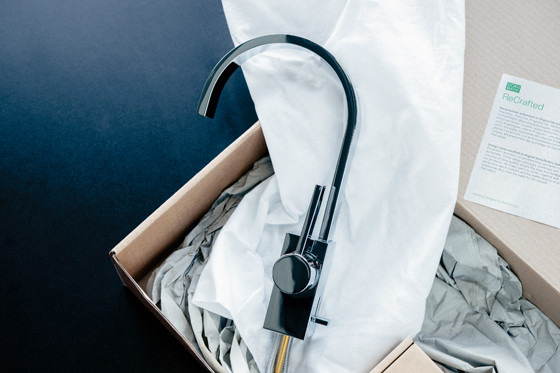
Dornbracht
Kundinnen und Kunden können ausgewählte Waschtisch-Armaturen in Chrom und Chrom-gebürstet erwerben. Zu den wiederaufbereiteten Produkten gehören z.B. Muster aus Ausstellungen. Künftig sollen auch Armaturen aus Privathaushalten und Hotels zurückgenommen werden. Nach Berechnungen des TÜV Rheinland werden im Vergleich zu einem Neuprodukt pro Armatur rund 40 % an CO2-Emissionen eingespart.
Stefan Gesing, CEO bei Dornbracht: „Mit dem Kauf einer Recrafted-Armatur geben unsere Kundinnen und Kunden zeitlosen Design-Klassikern ein neues Zuhause und handeln damit gleichzeitig umweltbewusst. Dabei stehen der Werterhalt der Produkte und ein minimierter Ressourceneinsatz im Vordergrund. Unabhängig davon bewahren wir mit dem Projekt aber auch immaterielle Werte, wie die handwerklichen Fähigkeiten, die in unserer Manufaktur seit Jahrzehnten weitergegeben werden.“
Hier gehts zum Recrafted-Shop
Recrafted-Prozesse werden in die Dornbracht-Produktion in Iserlohn in bestehende Abläufe eingebunden. Erfahrung in der Aufarbeitung gebrauchter Armaturen hat das Unternehmen bereits durch seinen Service: In der Abteilung werden seit mehr als 70 Jahren maßgefertigte Kundenwünsche realisiert – inklusive der Instandsetzung alter Armaturen.
In 7 Produktionsschritten zur Recrafted-Armatur
Von der gebrauchten Armatur zum wiederaufbereiteten Original: Der Prozess, den eine Recrafted-Armatur von Dornbracht durchläuft, ist geprägt durch handwerkliches Arbeiten und die Expertise der Fachkräfte am Standort in Iserlohn. Vom Demontieren über das Schleifen und Neu-Veredeln bis hin zum Verpacken – jeder einzelne Schritt dient der Werterhaltung.
1. Demontieren
Im ersten Prozess-Schritt, der Demontage, wird die zurückgenommene Armatur in ihre Einzelteile zerlegt. Nach der Sichtung der Komponenten wird zwischen Recrafted- und Recycling-Teilen getrennt. Anschließend wird das Restmaterial sortiert und über regionale Partner dem Recycling-Kreislauf zugeführt.
2. Entschichten des Armaturenkörpers
Im nächsten Schritt werden die wertvollen Messingkörper auf Galvanikgestelle aufgesteckt. Bei der elektrolytischen Entschichtung werden die Oberflächenrohstoffe, wie beispielsweise Gold, zurückgewonnen.
3. Schleifen, Polieren und Bürsten
Anschließend wird die Oberfläche in Handarbeit aufbereitet: Beim Schleifen werden Unebenheiten auf der Oberfläche des Werkstücks entfernt. Beim Führen der Schleifbänder mit Kontaktscheiben bedarf es einer perfekten Kombination aus Anpressdruck und Schnittgeschwindigkeit. Feine Schleifkörner werden beim Polieren über eine Paste auf eine Baumwollscheibe aufgetragen. Durch die Reibung zwischen dem Armaturenkörper und der Scheibe und die so entstehende Hitze schmelzen die Erhebungen auf dem Bauteil. Das Ergebnis ist eine stark reflektierende und hochglänzende Oberfläche. Für ein mattes Finish wird eine gradlinige, geordnete Bürststruktur, die durch eine technische Zeichnung vorgegeben ist, auf dem Bauteil aufgebracht. Dazu wird beispielsweise eine Trägerscheibe aus Baumwolle in Kombination mit einer speziellen Mattier-Paste oder ein Vliesband verwendet.
4. Veredeln der Oberfläche
Vom rohen Körper zum Edelmetall: In der Galvanik wird der Armaturenkörper neu veredelt. Die entstehende Oberfläche zeichnet sich durch Farbtiefe und Brillanz aus.
5. Lasern
Beim Lasern wird die Armatur mit dem Dornbracht Recrafted-Logo gekennzeichnet. So ist eindeutig erkennbar, dass es sich bei dem Produkt um ein wiederaufbereitetes Original handelt.
6. Kommissionieren
Bei der Kommissionierung wird der Armaturenkörper um die benötigten neuen Bauteile ergänzt. So werden beispielsweise Mischerkartuschen, Dichtungen und Strahlregler hinzugefügt.
7. Montieren und Verpacken
Während des letzten Prozess-Schrittes, der Montage, wird die Armatur vollständig zusammengebaut. Anschließend durchläuft sie eine Dichtigkeits- und eine abschließende Qualitätsprüfung. Zuletzt wird das Produkt gemeinsam mit dem Dornbracht Recrafted-Zertifikat in einer ökologischen Versandkartonage verpackt.
Recrafted ist Teil eines ganzheitlichen Nachhaltigkeitskonzepts
Das neue Recrafted-Konzept von Dornbracht ist Teil eines ganzheitlichen Nachhaltigkeitsansatzes, den das Unternehmen seit seiner Gründung im Jahr 1950 verfolgt. Denn Langlebigkeit und zeitloses Design sind seit jeher Grundprinzipien bei der Entwicklung und Produktion von Dornbracht-Armaturen. Ein weiterer elementarer Baustein ist das Lieferketten-Management. Es ist auf kurze Lieferwege ausgelegt: Das Unternehmen bezieht 80 % seiner Rohstoffe und Materialien aus Deutschland und 98 % aus Europa. Der überwiegende Teil der Vorprodukte kommt aus einem Umkreis von weniger als 200 km. Dieser Ansatz ist nicht nur nachhaltig, sondern sichert auch Arbeitsplätze in der Region Südwestfalen. Im Jahr 2015 hat Dornbracht zudem ein Energie-Management-System nach ISO 50001 eingeführt und konnte bereits 1,7 Mio. kWh pro Jahr einsparen. Seit Ende 2021 stammt der gesamte Strom des Dornbracht-Stammsitzes ausschließlich aus erneuerbaren Energien. In 2022 hat Dornbracht zudem die Neuzertifizierung der Umweltmanagement-Norm ISO 14001 erreicht. ■